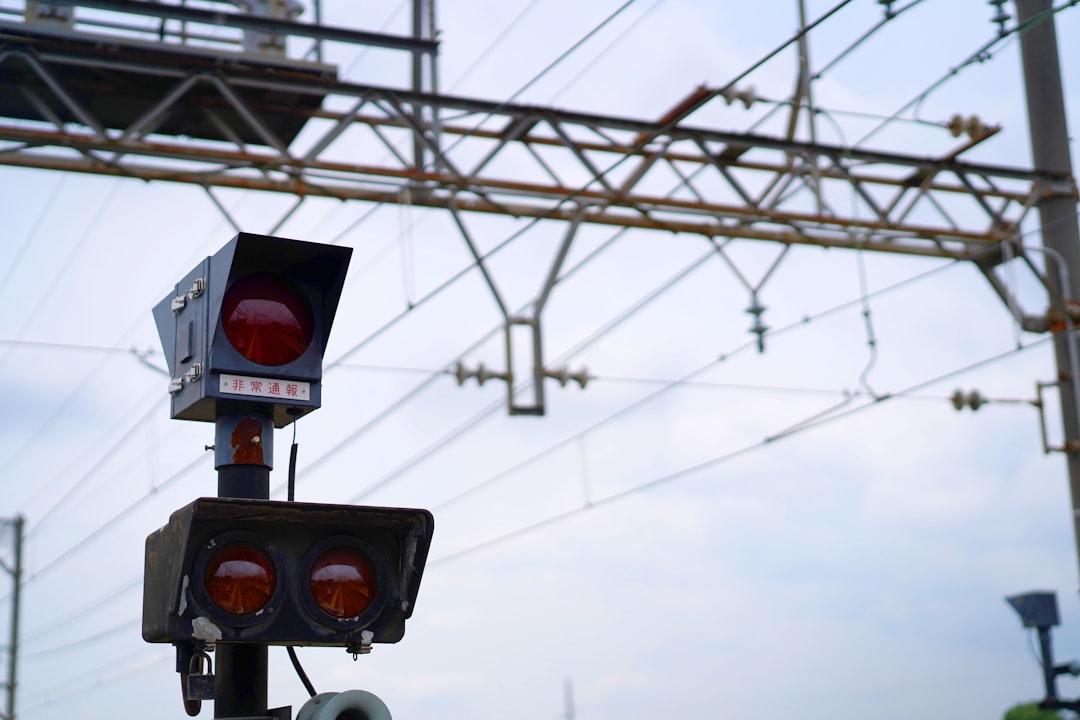
Workplace safety is a critical aspect of organizational management, applicable to all businesses regardless of their scale or sector. Prioritizing employee safety and well-being not only protects workers from potential harm but also fosters a positive work environment and enhances productivity. When employees perceive their workplace as safe, they tend to exhibit higher levels of engagement, motivation, and concentration on their tasks.
This often results in increased job satisfaction and reduced employee turnover. Moreover, a strong focus on workplace safety can significantly reduce the occurrence of costly accidents and injuries, which can have substantial financial implications for a company. By investing in safety measures and cultivating a safety-oriented culture, organizations can minimize workplace incidents and promote long-term business sustainability and success.
Prioritizing workplace safety is not only an ethical and legal requirement but also a strategic business decision. Adhering to safety regulations and standards protects employees and shields the organization from potential legal and financial consequences. Non-compliance with safety guidelines can lead to fines, legal actions, and reputational damage.
Conversely, a demonstrated commitment to workplace safety can enhance an organization’s public image, attract skilled professionals, and build trust with customers and stakeholders. In essence, workplace safety is a fundamental component of a company’s overall success and should be a primary concern for all organizations.
Key Takeaways
- Workplace safety is crucial for the well-being of employees and the success of a business.
- OSHA standards and regulations provide guidelines for maintaining a safe work environment.
- Developing safety procedures tailored to the specific needs of the workplace is essential for accident prevention.
- Training and education of employees on safety protocols is key to ensuring a safe work environment.
- Implementing safety equipment and tools, such as personal protective equipment, is necessary to minimize workplace hazards.
OSHA Standards and Regulations
OSHA Regulations: Protecting Employees from Workplace Dangers
OSHA regulations are designed to protect employees from potential dangers in the workplace and require employers to provide a safe and healthy work environment. It is essential for organizations to familiarize themselves with OSHA standards relevant to their industry and ensure compliance to avoid penalties and protect their workforce.
OSHA Resources: Empowering Employers and Employees
In addition to setting standards, OSHA also provides training, outreach, education, and assistance to both employers and employees. This includes resources for developing safety programs, conducting workplace assessments, and implementing best practices for hazard prevention.
Benefits of OSHA Compliance: A Safer Work Environment
By adhering to OSHA regulations and taking advantage of the resources they provide, organizations can create a safer work environment, reduce the risk of accidents, and demonstrate their commitment to employee well-being.
Developing Safety Procedures
Developing comprehensive safety procedures is essential for mitigating workplace hazards and ensuring the well-being of employees. Safety procedures should be tailored to the specific needs and risks present in the organization’s work environment. This may include protocols for handling hazardous materials, operating machinery, responding to emergencies, and preventing common workplace injuries.
It is important for organizations to involve employees in the development of safety procedures to ensure that they are practical, effective, and reflective of the actual work conditions. Furthermore, safety procedures should be clearly documented, easily accessible, and regularly reviewed and updated as needed. This ensures that employees are aware of the protocols in place and that any changes in the work environment or regulations are promptly addressed.
By establishing robust safety procedures, organizations can minimize the potential for accidents, injuries, and occupational illnesses, creating a safer and more secure workplace for all.
Training and Education
Training and Education Metrics | 2019 | 2020 | 2021 |
---|---|---|---|
Number of Training Sessions | 150 | 180 | 200 |
Training Hours per Employee | 20 | 25 | 30 |
Employee Satisfaction with Training | 85% | 90% | 92% |
Providing comprehensive training and education on workplace safety is crucial for ensuring that employees are equipped with the knowledge and skills to identify hazards and prevent accidents. Training should cover a wide range of topics, including but not limited to, proper equipment usage, emergency response protocols, ergonomics, chemical safety, and personal protective equipment (PPE) usage. It is important for organizations to provide initial training for new employees as well as ongoing refresher courses to reinforce safety best practices.
In addition to general safety training, specialized training may be necessary for employees working in specific roles or with unique hazards. For example, employees working with heavy machinery may require specialized training on equipment operation and maintenance. By investing in comprehensive training and education programs, organizations can empower their employees to prioritize safety in their daily tasks and contribute to a safer work environment overall.
Implementing Safety Equipment and Tools
Implementing appropriate safety equipment and tools is essential for protecting employees from workplace hazards. This may include providing personal protective equipment (PPE) such as gloves, goggles, helmets, or respirators to mitigate exposure to physical or chemical hazards. Additionally, organizations should ensure that machinery and equipment are properly maintained and equipped with necessary safety features such as guards, emergency shut-off switches, or warning systems.
Furthermore, implementing ergonomic tools and equipment can help prevent musculoskeletal injuries and improve overall employee well-being. This may include adjustable workstations, lifting aids, or tools designed to reduce repetitive strain injuries. By prioritizing the implementation of safety equipment and tools, organizations can create a safer work environment and reduce the risk of workplace accidents.
Regular Safety Inspections and Audits
Conducting regular safety inspections and audits is essential for identifying potential hazards, assessing the effectiveness of safety measures, and ensuring compliance with regulations. Inspections should be thorough and systematic, covering all areas of the workplace including equipment, machinery, storage areas, emergency exits, and common work areas. By identifying potential hazards early on, organizations can take proactive measures to address them before they escalate into serious incidents.
In addition to internal inspections, organizations may also benefit from third-party audits or consultations to gain an outside perspective on their safety practices. This can help identify blind spots or areas for improvement that may have been overlooked internally. By conducting regular safety inspections and audits, organizations can demonstrate their commitment to workplace safety while proactively addressing potential risks.
Reporting and Responding to Safety Incidents
Establishing clear protocols for reporting and responding to safety incidents is crucial for addressing accidents or near misses promptly and effectively. Employees should be encouraged to report any unsafe conditions or incidents they encounter without fear of retaliation. Additionally, organizations should have a clear process in place for investigating incidents, identifying root causes, and implementing corrective actions to prevent similar incidents from occurring in the future.
Furthermore, organizations should maintain accurate records of all safety incidents and near misses to identify trends or patterns that may indicate underlying issues that need to be addressed. By responding promptly to safety incidents and implementing corrective actions, organizations can create a culture of continuous improvement in workplace safety while minimizing the risk of future accidents. In conclusion, workplace safety is an essential aspect of any organization’s operations that cannot be overlooked.
Prioritizing workplace safety not only protects employees from harm but also contributes to a positive work environment and increased productivity. By adhering to OSHA standards and regulations, developing comprehensive safety procedures, providing training and education, implementing safety equipment and tools, conducting regular safety inspections and audits, as well as establishing clear protocols for reporting and responding to safety incidents, organizations can create a safer work environment while demonstrating their commitment to employee well-being. Ultimately, investing in workplace safety is not only a moral imperative but also a strategic business decision that can lead to long-term success and sustainability.
If you are interested in learning more about work-related safety standards and procedures, you may also want to check out this article on janitors and building cleaners. This article discusses the importance of safety protocols and procedures for those working in the cleaning industry, highlighting the need for proper training and equipment to prevent workplace accidents and injuries. Understanding the specific safety concerns and regulations within different industries can help ensure a safe and healthy work environment for all employees.
FAQs
What are work-related safety standards?
Work-related safety standards are a set of guidelines and regulations established by government agencies or industry organizations to ensure the safety and health of employees in the workplace. These standards cover a wide range of topics including equipment safety, chemical handling, emergency procedures, and more.
Why are work-related safety standards important?
Work-related safety standards are important because they help prevent workplace accidents, injuries, and illnesses. By following these standards, employers can create a safe and healthy work environment for their employees, reducing the risk of costly incidents and promoting overall well-being.
What are some common work-related safety procedures?
Common work-related safety procedures include conducting regular safety training for employees, providing personal protective equipment (PPE), implementing emergency response plans, conducting regular equipment inspections, and maintaining a clean and organized work environment.
Who is responsible for enforcing work-related safety standards?
Work-related safety standards are enforced by government agencies such as the Occupational Safety and Health Administration (OSHA) in the United States. Employers are responsible for ensuring that their workplace complies with these standards and are subject to inspections and penalties for non-compliance.
How can employees contribute to work-related safety?
Employees can contribute to work-related safety by following safety procedures and guidelines, reporting any hazards or unsafe conditions to their supervisors, participating in safety training programs, and using personal protective equipment as required. It is important for employees to be proactive in maintaining a safe work environment.